Flexibility and Agility in Manufacturing Systems
Flexibility: Flexibility entails to produce equitably priced customized products of superior quality that can be rapidly delivered to clienteles. In manufacturing system flexibility refers to the capability of producing different parts without major retooling and it is a measure of how fast the company converts its process from making an old line of products to produce a new product. Flexibility is the ability to change a production schedule, to change a part, or to handle multiple parts. Flexible manufacturing systems are technologies that combine the benefits of both computers and numerical control machine tools. They have been addressed as the solution to challenges that manufacturing industries facing at global scale.
Reviewing the past literature, it is found that notion of flexibility in manufacturing system was extensively studied overtime. The concept of flexible manufacturing systems grew during the 1960's when robots, programmable controllers, and computerized numerical controls brought an environment to the factory floor in the form of numerically-controlled and direct-numerically-controlled machines. It was initially defined as a manufacturing system's ability to respond to changes in customer requirements without penalizing, cost, time effort and performance to any great degree (Upton, 1994). Several theorists stated that flexibility is necessary element for coping with internal and external disturbances. It can also be seen as measurement for numerous product variants that manufacturing system can manage. The measurement of flexibility cannot be performed on an absolute scale but must be seen as a relative measure (Mitsuishi, et, al., 2008).
The main objective of a flexible manufacturing system is to offer the speed needed to change with market conditions quickly, but not sacrifice any quality.
Flexibility studies have focused on production environments and inter organizational elements such as mix, volume, and product and production routes. Sharifi and Zhang determined that flexibility was not sufficient to address new market challenges market by intense competitive environment (1999). It also provided the research theoretical model linking flexible manufacturing competencies with volume flexibility, mix flexibility and customer satisfaction (Tullio Tolio, 2008).
Framework proposed by Zhang, et, al. (Source: Tullio Tolio, 2008)
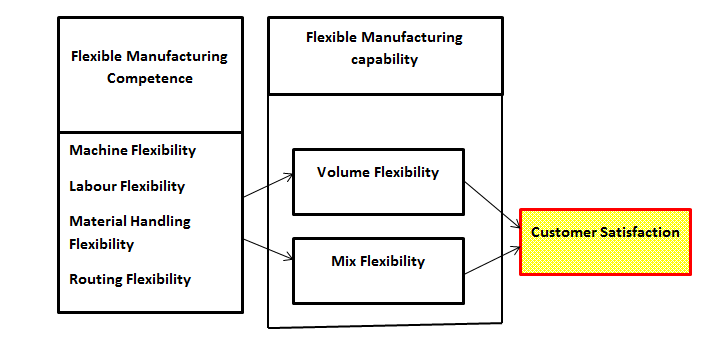
Browne et al., 1984 defines flexibility in manufacturing system as an integrated computer-controlled system with automated material handling devices and CNC machine-tools and which can be used to simultaneously process a medium-sized volume of a variety of parts. Chan et al. (2007) offered a simulation study using Taguchi's method analysis of physical and operating parameters of the flexible manufacturing system along with flexibility. An approach is developed to study the impact of variations in the physical and operating parameters of flexibility in manufacturing system and to identify the level of these variations. The physical and operating parameters of alternative resources may influence the system's performance with the changing levels of flexibility and operational control parameters such as scheduling rules. Various results of simulation study demonstrates that predictable benefits may not be present when routing flexibility levels are increased with presence of the variations in physical and operating parameters. The increase in routing flexibility level becomes counterproductive under such environment when variations are above certain limits. It may be useful for decision maker to distinguish the level of flexibility up to which it can be gainfully increased under the presence of variations.
Sarker et al. (1994) have offered a thorough classification for the types of manufacturing related flexibility as follows: Routing flexibility, machine, flexibility, process flexibility, expansion flexibility, job flexibility, design flexibility, material handling flexibility, setup time flexibility, and volume flexibility. Bolwijn and Kumpe (1990) and De Meyer et al. (1989) have recognized flexibility' as the focus of the next competitive battle.
Other group of theorists also explained the notion of flexibility in their terms. Gupta and Buzacott (1989) elucidated that the flexibility does not come from the abilities of machine alone. Actually flexibility is the consequence of amalgamation of factors like physical characteristics, operating decisions, information integration, and management practice. Flexibility is critical in providing the effectiveness to manufacturing system under different operating conditions. Bennett et al. (1992) recognises the factors crucial to the development of efficient flexible production systems, namely: effective integration of subsystems, development of appropriate controls and performance measures, compatibility between production system design and organization structure, and argues that the flexibility cannot be potentially exploited if its objectives are not defined and considered at design stage. Kumar et al. (2003) used an ant colony optimization approach for scheduling of flexibility in manufacturing system for a given level of flexibility. Wang and Yen (2001) measured the transportation times in automated material handling system for simulation study of dispatching rule performance.
Though there is confusion among theorists about occurrence of flexibility. Gerwin (1993) proposes that the lack of clear understanding of manufacturing flexibility is inhibiting progress towards the utilization of flexibility concepts in industry and hindering manufacturing managers from evaluating and changing the flexibility of their operations. Gunasekaran et al. (1993) and Gerwin (1993) recognised the measurement of flexibility and performance as an important obstacle to realize a full comprehension of flexible manufacturing system behaviour.
Vast amount of theoretical studies have focused on the concept of flexibility in manufacturing system. Flexible manufacturing system is a class of manufacturing system that can be speedily configured to produce various products. Since last few decades, the modelling and the analysis of flexibility in manufacturing system has been closely studied by control theorists and engineers. A flexibility in manufacturing system is a production system where a discrete number of raw parts are processed and assembled by controlled machines, computers and/or robots (Ruiz et al., 2009).
There are three abilities that a manufacturing system must retain in order to be flexible:
- The ability to identify and distinguish among different incoming part or product styles processed by the system.
- Quick changeover of operating instructions.
- Quick changeover of physical setup.
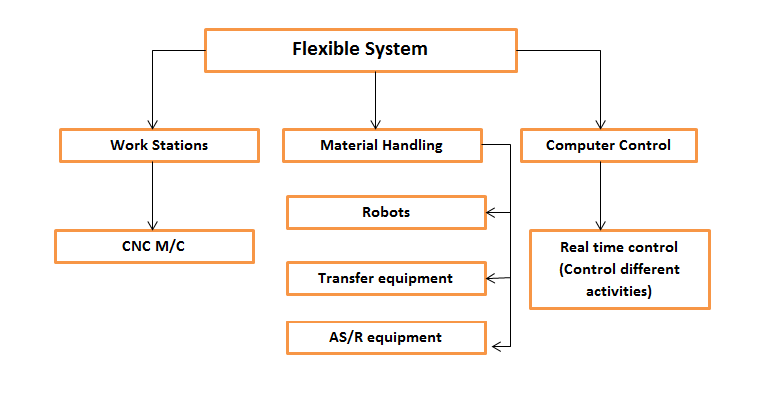
The classification of flexibility types established by Browne et al. (1984) who has formed the foundation of most consequent research into measuring manufacturing flexibility
It has been recognised in literature that there are three levels of manufacturing flexibility.
1. Basic flexibilities:
Machine flexibility: It basically refers to the various types of operations that the machine can perform without requiring prohibitive effort in switching from one operation to another (Sethi and Sethi, 1990).
Material handling flexibility: A measure of the ease with which different part types can be transported and properly positioned at the various machine tools in a system.
Operation flexibility: A measure of the ease with which alternative operation sequences can be used for processing a part type. It is the ability to interchange the sequence of manufacturing operations for a given part.
2. System flexibilities:
Volume flexibility: A measure of a system's capability to be operated profitably at different volumes of the existing part types. It is the ability to operate profitably at different production volume.
Expansion flexibility: The ability to build a system and expand it incrementally. It is the ability to expand the capacity of the system as needed, easily and modularly.
Routing flexibility: A measure of the alternative paths that a part can effectively follow through a system for a given process plan. It is the ability to vary the path a part may take through the manufacturing system.
Process flexibility: A measure of the volume of the set of part types that a system can produce without incurring any setup. It is the ability to change between the productions of different products with minimal delay.
Product flexibility: The volume of the set of part types that can be manufactured in a system with minor setup. It is the ability to change the mix of products in current production, also known as mix-change flexibility (Carter, 1986).
3. Aggregate flexibilities:
Program flexibility: The ability of a system to run for reasonably long periods without external intervention.
Production flexibility: The volume of the set of part types that a system can produce without major investment in capital equipment.
Market flexibility: The ability of a system to efficiently adapt to changing market conditions.
Table: Types of flexibility in manufacturing
Flexibility Type |
Definition |
Depends on factors such as |
Machine Flexibility |
Capacity to adapt a given machine (work station) in the system to wide range of production operations and part styles. The greater the range of operations and part styles, the greater the machine flexibility. |
Setup or changeover time. |
Production Flexibility |
The range or universe of part styles that can be produced on the system. |
Machine flexibility of individual stations. Range of maching flexibilities of all stations in the system. |
Mix Flexibility |
Ability to change the product mis while maintaining same total production quatity that is producing the same parts only in different proportions. |
Similarity of parts in the mix. Relative work content times of parts produced. Machine flexibility. |
Product Flexibility |
Ease with which design changes can be accomodated. Ease with which new products can be introduced. |
How closely now part design matches the existing part family. |
Routing Flexibility |
Capcity to produce parts through alternative work station sequences in response to equipment breakdowns, toools failures and other intruptions at individual stations. |
Similarity of parts in the mix.Similarity of work stations. |
Volum.e Flexibility |
Ability to economically produce parts in high and low total quantities of production, given the fixed investment in the system |
Level of manual labour performing production. |
Expansion Flexibility |
Ease with which the system can be expanded to increase total production quantities. |
Expense of adding workstations. |
In order to qualify as being flexible, the automated system should clear four tests:
- Part variety test.
- Schedule change test.
- Error recovery test.
- New part test.
In recent years, the flexibility manufacturing system has arisen as one of the upheavals in the manufacturing industries. It has made it conceivable to produce a variety of parts in less time and cost. The use of FMS in the current market setting can satisfy the increasing demands of variety, quantity and speed at the same time. The components of the flexibility manufacturing system can be categorized in to two parts:
1. Hardware: Machine tools, handling systems, guided vehicles, inspection centre, robots, etc.
2. Software: Software for FMS can further be classified into extrinsic and intrinsic functions.
Major benefits of a flexible manufacturing system is the change to adapt the operation to fulfil emerging demands for certain products by customers. Flexibility in manufacturing system enable the business to capture a significant market share and increase revenues for as long as the demand for those products remains in place. Another benefit of a flexible manufacturing system is the chance to minimize labour costs during seasonal recessions, and then increase the labour force during busy seasons. This approach can be realised by cross training employees who can take on additional responsibilities during lean seasons, then turn a portion of those responsibilities over to part-time personnel during busy seasons. The end result is well-organized operation that still helps to keep the cost of production for each unit produced under a certain level.
Main drawback of flexible manufacturing system is that this type of arrangement often has a significant up-front cost, since machinery may have to be modified to allow for an easier conversion of goods produced. This process often lead to changing the corporate culture, a process that can take a lot of time and result in some loss of efficiency in the short-term. Technological barriers may also slow the efforts to be more adaptable, requiring additional planning to overcome those obstacles and creating additional expense for the company. Many researches raised concern that this type of system can only handle a relatively-narrow range of part varieties, so it must be used for similar parts that require similar processing. Due to increased intricacy and cost, flexible manufacturing system also requires a longer planning and development period than traditional manufacturing equipment.
It can be said that initiation of focused flexibility may represent an important means to rationalize the way by which flexibility is embedded in manufacturing system. Flexible manufacturing systems are extensively used to improve productivity and quality of the product. It also improves the quality of life for the operator. The new techniques will have a major impact on economic factors.
Agility:
Manufacturing agility is evolved as an essential capability for organisations to handle uncertainties in rapidly changing business climate. Though manufacturing agility is highly valuable for companies but little empirical researches have done to elucidate its construct. Agile manufacturing has been progressively viewed as a persuasive strategy. Agile manufacturing is an incorporation of technologies, people, facilities, information systems and business processes. The manufacturing agility metric is problematic to develop due to its multidimensional and uncertain nature. Agility is basically vital concept if the manufactures have to stay competitive within a highly unstable marketplace. Abundant of literatures have suggested the notion of manufacturing agility capabilities to quickly respond to the market instabilities (Glodman, et, al., 1996). Agile manufacturing is described by many theorists as the capability of surviving and prospering in a competitive environment of continuous and unpredictable change by reacting quickly and effectively to changing markets, driven by customer designed high-quality, high-performance, products and services.
It is often involved a speed of changes in process, or system without compromising daily operations or subsequent change processes. Progressively, the manufacturing enterprises have paid more attention to enhance their performance through manufacturing agility implementation (Narasimhana, Swinka, and Kimb, 2006). Agile manufacturing was developed as an alternative response to business challenges. It is described by numerous experts as ability of production management to address unforeseen market requirements and accomplish competitive advantage (Management Association, 2012).
The concept of manufacturing agility, as a part of agility viewpoint involves the development of manufacturing capabilities to realize continuous competitive advantage under changeable business environment. The origin of agility as a business concept can be traced back from flexibility manufacturing system (Christopher, 2000). Research studies have revealed that manufacturing agility was first recognised by Goldman, Nagel, Preiss and Dove in their 21st Century Manufacturing Enterprise Strategy report at Iacocca Institute of Lehigh University. This multifaceted concept was studied by various authors.
Vast amount of literature is available to describe the phrase agile manufacturing. Agility is the measure of a manufacturer's ability to react fast to sudden, unpredictable change in customer demand for its products and services and make a profit (Noaker, 1994). Industries are embracing the concepts of agile manufacturing, which favour nimble principles over the aging techniques of mass production (O'Connor, 1994). In expert's view, Agile manufacturing is explained as the ability to produce so-called custom-engineered or custom-specific parts usually in short production runs or one-of-a-kind batches. Other theorists define agility as the ability to accomplish rapid changeover between the manufacture of different assemblies utilizing essentially the same workcell and allow the rapid introduction of new products with little or no workcell downtime. It has been documented in theoretical studies that agile manufacturing is a response to complexity brought about by constant change. Lean is a collection of operational techniques focused on productive use of resources. Agility is an overall strategy focused on thriving in an unpredictable environment. Focusing on the individual customer, agile competition has evolved from the unilateral producer-centred customer-responsive companies inspired by the lean manufacturing refinement of mass production to interactive producer-customer relationships (Goldman et al., 1994).
Prime objectives of manufacturing agility include customer enrichment through one of-a- kind products at the cost of mass production, organising to master change by competing from multiple fronts with reconfigurable resources, intra and inter-enterprise cooperation and leveraging of enterprise knowledge by means of advanced technologies. These principles are important as sources of contemporary competitive advantage constructs.
There several reasons to become agile that include Global Competition is intensifying, mass markets are fragmenting into niche markets, cooperation among companies is becoming necessary, including companies who are in direct competition with each other, customers are expecting, low volume products, high quality products, custom products, very short product life-cycles, development time, and production lead times are required and customers want to be treated as individuals.
Characteristics of agile manufacturing to manage change are as under:
Recognition: The first step to manage change is to identify that it is happening and proactively engage in change management. They can conduct a company-wide knowledge audit.
Focus on the customer: Company must focus on improving the customer's experience instead of allowing change to control business. Customers want solutions that comprise both products and services, product flexibility and variability to meet their demands, and a quick response to questions that relate to pricing and support.
Leveraging resources: An agile enterprise can also be recognized by its ability to effectively exploit its resources and share knowledge. Part of change management is to identify underutilized, unused or non-existent resources and take better advantage of them or bring them on board.
Cooperating to compete: Lastly, agile manufacturers change the way that they interact with their business partners so that they can compete more effectively through cooperation. They know that they do not dictate market demands, they listens to their customers, find core competence, make partnerships and share knowledge when it is necessary to provide the customer with a solution.
It has been demonstrated in bulk of studies that agile manufacturing is an emerging concept in industries that aims to achieve manufacturing flexibility and responsiveness in changing market needs. Agile manufacturing system can be conceptually thought of as being an integrated whole of complex interactive sub systems, organized in such a way as to endeavour toward common set of goals (Merchant, 1984). Due to inherent complexities and agile associated with modern manufacturing system, modelling these interactive subsystem using common analytical and mathematical approach has proved to be very difficult. Agile manufacturing system is a multi-objective seeking system. An uppermost level, Agile manufacturing system takes the customer needs, feedback, and part of society's total energy information then transform them in such a way as to produce the output more efficiently (Gunasekaran , 2001).
Functional scheme of an Agile manufacturing system (Source: Gunasekaran , 2001)
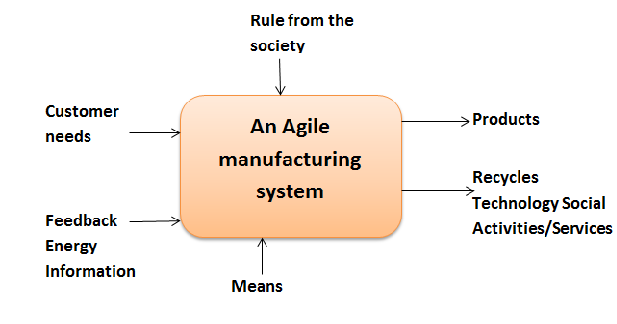
In Agile manufacturing system, according to dynamic customer request, along with the feedback from system, the product conceptual design is done and there is a great need for product innovation. Subsequently the product is configured and parameterized. Product manufacturability is considered and tested with simulation tools. In most advanced Agile manufacturing environment, completely and semi-autonomous systems are used. In order to ensure that the Agile manufacturing process is under good control, it is necessary to monitor the process, obtain process and product information, diagnose the problems and control the process (Gunasekaran , 2001).
Abundant of management reports signify that Agility enables enterprises to succeed in an environment of continuous and unexpected change (Richards 1996). Researchers have approached the management of agile manufacturing from a various viewpoints using a wide range of tools. The enablers of agile manufacturing include virtual enterprise, formation tools/metrics, physically distributed teams and manufacturing, rapid partnership formation tools/metrics, concurrent engineering, integrated product/production/business information system, rapid prototyping tools and electronic commerce.
Enablers of agile manufacturing
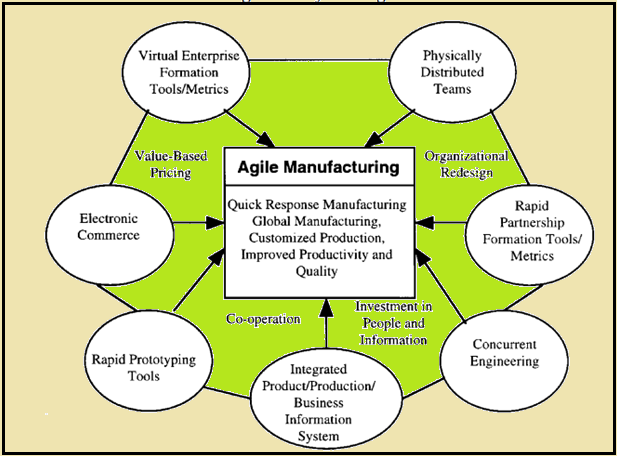
In above figure, a conceptual model has been presented to illustrate the enablers of agile manufacturing. To realize agility in manufacturing, physically distributed firms need to be incorporated and managed efficiently so that the system is able to adjust to varying market conditions. It can be understood from the conceptual model that different enablers of agile manufacturing are overlying each other. Therefore, all the enablers should be integrated to achieve good integration.
Agile manufacturing is a new, post-mass-production system to develop and distribute goods and services. Agile manufacturing necessitates resources that are beyond the reach of a single company. It is imperative for firms to share resources and technologies. The competitive ability of an enterprise depends on its ability to establish good relationships, and thus cooperation seems to be the key to possibly complementary relationships.
Copious studies have demonstrated that agile production, the next phase in manufacturing, is the eventual requirement for global level manufacturing performance. Agility involves fundamental change in an organization's approach to cycle-time reduction. Agility involves cost and that cost must be feasible over the long run for a truly agile organization so that working capital is not eroded over the long run. The agile organization also changes constantly with time, becoming accustomed to change itself. Sturdiness, the ability to anticipate change and provide a well-ordered completion cycle is another metric of agility. Lastly, the scope of change must be capable of wide swings with little resistance. Scope is a measurement of the accommodation to magnitude of change. Agile organizations not only are aware of their normal coverings of production capability, but also exploit on change that goes beyond these normal scopes. Agile organizations go further than expecting a number of contingencies. The system itself can be disassembled and recreated as required. Therefore, agility goes beyond lean into arena of robustness and challenge. Agile manufacturing also consider the human condition by encouraging creativity from employees, while at the same time increasing the standard of living of society as a whole and the free time of those employed.
Advantages of Agile Manufacturing: Agile manufacturing has more benefits to organization. Supporters of agile model, Terrence Schmoyer, executive director of the Agile Manufacturing Enterprise Forum, stated that Agile manufacturing provides the ability to flourish and prosper in a competitive environment of continuous and unanticipated change and to respond rapidly to fluctuating markets. Other benefits of agile manufacturing include:
- Proactively response to customer needs leads to a successful organization.
- Highly flexible to changing environments and able to respond to environmental changes.
- Organizations gain capability to reorganize them self very quickly.
- Agile manufacturing can easily deal with contingencies which cannot be predicted.
- Very low inventories and costs involved with inventories are also reduced.
- Low lead time and flexible manufacturing quantities.
- Encourages creativity in employees thus leading to high job satisfaction.
- Superior product quality can be maintained.
Disadvantages of Agile manufacturing: Major drawbacks of agile manufacturing are mentioned below:
- Mass markets are fragmented into niche markets therefore difficult to accomplish economies of scale.
- Giant organizations have difficulty to adopt agile manufacturing as the constant changes prevent any fixed organization structure.
- High cost is involved in embracing agile production.
- Highly trained employees are needed which requires a lot of monetary and time investment.
- Major issue is the cooperation between competitor companies, which are almost impossible in Indian background.
- Main strength of organization lies in its human capital so much that abrasion could seriously weaken its future growth.
Today, agile manufacturing is gaining more attention from both the academic and industrial groups. Widespread programmes are being conducted on related issues to spread agile manufacturing concepts, to build agile enterprise prototypes, and eventually to realize an agile industry.
To summarize, Agile manufacturing systems are developed as a solution to a people with a changeable and dynamic demand, and with a high degree of mass customization in its products. The notion of agility was evolved in 1991 when an industry group observed that the growing rate of change in business environment was rapidly overtaking the ability of outmoded manufacturing organizations to adapt. Agile manufacturing is a technique for manufacturing which combine organization, people and technology into an integrated and synchronized entirely. It is a phrase applied to an organization that has created the processes, tools, and training to allow it to respond speedily to customer needs and market changes while still controlling costs and quality. It is the approach that many enterprises are using as a solution to the new market opportunities. Many studies have been done so far to elucidate the process and benefit of agile manufacturing.