Aggregate Production Planning
Aggregate production planning, abbreviated as APP, is useful for operation management. It is associated with the determination of production, inventory, and personnel levels to fulfil varying demand over a planning perspective that ranges from a period of six months to one year. Aggregate production plans are needed to exploit workforce opportunity and represent a crucial part of operations management. Aggregate production plans facilitate matching of supply and demand while reducing costs. Process of Aggregate production planning applies the upper-level predictions to lower-level, production-floor scheduling and is most successful when applied to periods 2 to 18 months in the future. Plans generally either "chase" demand, adjusting workforce accordingly, or are "level" plans, meaning that labour is comparatively constant with fluctuations in demand being met by inventories and back orders.
Concept of aggregate production planning denotes to the process of determine the overall quantities of products to be manufactured or produced in a plant or other manufacturing facility during a medium term planning period such as a month, or a quarter. The aggregate plan output comprises of the total quantities of each product or a group of product to be manufactured in the plan period of going into details of scheduling of different manufacturing activities required to attain the planned production levels. The aggregate production will also not specify details such as the dates when material ordered against individual customer order will be ready for delivery. The aggregate production plan is designed to establish overall production targets and as input for planning availability of other inputs and supporting activities to meet the production targets. The aggregate plans then form the basis of more comprehensive production such as daily and weekly production schedules and customer delivery schedules.
The prime objective of Aggregate Production Planning is to judge company policies and management inputs linked to operations, distribution and marketing, materials, accounting and finance, engineering and human resources to reduce the price and increase revenue, enhance customer service, lessen inventory investment, decrease changes in production rates, reduce changes in work-force levels, boost utilization of plant and equipment.
Costs relevant to aggregate production planning:
- Basic production costs: material costs, direct labour costs, and overhead costs. It is customary to divide these costs into variable and fixed costs.
- Costs associated with changes in the production rate: Costs involved in hiring, training, and laying off personnel, as well as overtime compensations.
- Inventory related costs. Aggregate production planning models may be supportive as decision support systems and to appraise proposals in union negotiations.
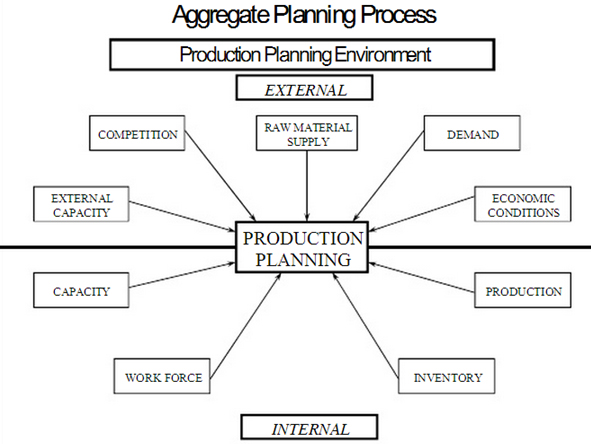
Techniques of Aggregate Planning
Various techniques are used to perform the task of aggregate planning. Usually, there are two categories: Informal trial-and-error techniques and mathematical techniques. In practice, informal techniques are more commonly used. However, a substantial amount of research has been done to mathematical techniques, but still, they are not as extensively used, they often serve as a basis for comparing the effectiveness of alternative techniques for aggregate planning.
There are several steps in general procedure for aggregate planning:
- Determine demand for each period.
- Determine capacities (regular time, overtime, subcontracting) for each period.
- Identify company or departmental policies that are pertinent (e.g., maintain a safety stock of 5 percent of demand, maintain a reasonably stable workforce).
- Determine unit costs for regular time, overtime, subcontracting, holding inventories, back orders, layoffs, and other relevant costs.
- Develop alternative plans and compute the cost for each activity.
- If satisfactory plans emerge, select the one that best satisfies objectives. Otherwise, return to step 5.
Procedure for Aggregate Planning
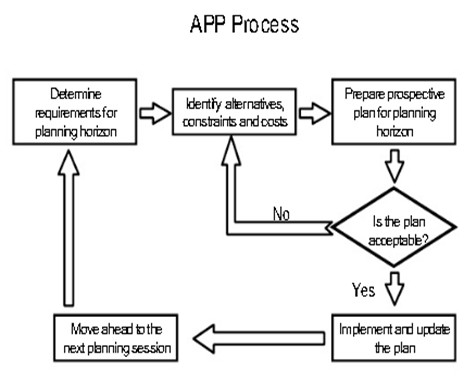
It can be useful to employ a worksheet or spreadsheet to summarize demand, capacity, and cost for each plan. Additionally, graphs can be used to guide development of alternatives. Among all methods, the spreadsheet solver approach is the most appropriate for industries because the solver on spreadsheet software is readily available on virtually all personal computers, the APP model is comparatively easy to devise in a spreadsheet format, and lastly, the results are easy to construe. There are certain guidelines for developing optimal aggregate production plan using spreadsheet solver. First of all, necessary data must be collected for developing Aggregate production planning mode. Secondly, formulate APP model in the spreadsheet format. Next step is to appraise the obtained solutions. This can be done by presenting the constructed spreadsheet aggregate production planning model and its solutions to related departments of the company such as production, personnel, planning, sales and marketing, and warehousing, and judge whether the solutions are satisfactory. The comparison between the existing aggregate production plan and the optimal plan generated from the Aggregate production planning model may be done in financial term. If the solution is not satisfactory, values of some input parameters may need to be reconsidered or the constraints may need to be customized. The spreadsheet APP model will be changed until the solutions are acceptable. Last step is to implement the aggregate production plan. After the spreadsheet APP model is agreeably developed and solved, the obtained solutions can be implemented. During the execution of the aggregate production plan, some parameters of the model may be altered such as demands, productivity rates, related costs, number of workers, and inventory levels. These parameters should be modernized regularly and the APP model is solved to resolve the revised aggregate production plan.
Steps for Developing the Aggregate Production Plan
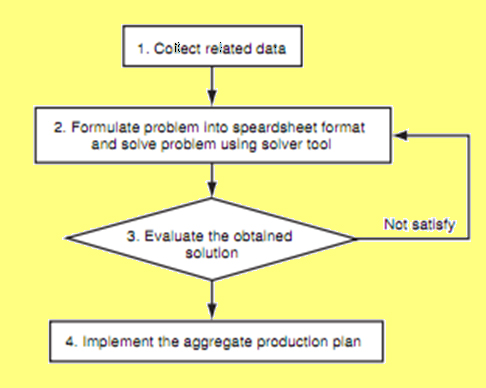
To summarize, aggregate production planning, is an effectual approach to operations management and concentrate to satisfy demand as it relates to production, labour force, inventory and other models. Aggregate production planning can attach in facility planning with scheduling decisions. Aggregate production planning assists to lessen production costs, the effect of variant demand, cost of inventory and labour costs. Aggregate production planning also exploits plant and equipment utilization and profits. The efficiency of aggregate production planning is a production plan that indicates how many workers are needed in each period, the amount and type of production (such as regular, overtime, subcontracting, etc.), and the units to be produced, stored, and back ordered per month or per quarter. Aggregate production planning is also a constructive tool to create and assess alternatives such as the adjustment of the labour force through hire/fire/layoff/overtime, the use of subcontractors, anticipatory inventory, and even the development of corresponding products and pricing strategies.