Equipment Replacement And Maintenance
Organizations use equipment in production and testing which must be maintained or replaced on planned basis. Manufacturing industries are facing fierce competition therefore companies invest in highly automated production system with good quality equipment. It is necessary to utilize equipment in best way to stay in the global market, and maintain the production operation thus leading to the economical sustainability as well as increase company profit. When an unplanned interruption occurs due to machines or equipment failure, this disturbs the production operation.
Equipment Replacement
The replacement of productive equipment is important strategic decisions faced by both manufacturing and service firms because purchasing a new piece of equipment often involves more cost and can affect the productivity and effectiveness of the firm. Currently, this issue is highlighted in fast changing technologies and good equipment purchase can soon become obsolete. Under these situations, the driving motivation to take replacement decisions is likely to be technological outmodedness instead of physical deterioration, of the existing equipment. This situation is typical of microcomputers, computerized numerically controlled machines, and other electronics technologies.Bulk of management studies have been done in equipment replacement. The customary approach to the equipment replacement problem emphasizes the physical deterioration of the existing equipment. The main concept is to replace the equipment when the cost of operating and maintaining it become sufficiently high, in net expected present value terms, to substantiate a replacement. In most conventional models, technology is supposed to remain constant over time (Derman, and Hatoyama, 1984). The approach of Derman, and Hatoyama would lead to inappropriate decisions if technology does change. Currently, researchers started to model the equipment replacement problem due to technological change under vagueness. Goldstein, Ladany and Mehrez introduce uncertainty using stationary forecasts. Hopp and Nair developed a model using non-stationary technology forecasts but where the revenue generated by various technologies is different but constant over time (1991).
The replacement problems are associated with the issues that develops when the performance of an item decreases, failure or breakdown occurs. The decline in performance or breakdown may be gradual or sometimes sudden. There is a need for replacement of items when;
- The existing item or system has become inefficient or require more maintenance.
- The existing equipment has failed due to accident or otherwise and does not work at all.
- The existing equipment is expected to fail shortly.
- The existing equipment has become obsolete due to the availability of equipment with latest technology and better design. The solution to replacement problem is to device best policy that determines the time at which the replacement is most economical instead of continuing at an increased maintenance cost.
The Main objective of replacement policy is to guide the organization in many situations so that it can take correct decision such in a situations when waiting for complete failure of item or to replace earlier at the expense of higher cost of the item, whether to replace the underperforming equipment with the similar kind of item or by different kind of item. The problem of replacement occurs in the case of both men and machines.
There are numerous reasons for equipment replacement. The first reason is the equipment is depleted of function. Second reason for replacing equipment is if the equipment becomes obsolete. For example, older computers are much slower and have fewer features than their modern counterparts. In addition, older computers are harder to maintain because replacement parts and qualified technicians are much harder to find. Another reason for replacement is deterioration due to aging. Equipment is inadequate and does not meet needs, increased demand. Then it is replaced with a larger asset.
There are many types of failure in equipment:
- Gradual Failure: In this, the failure mechanism is progressive. As an equipment becomes old, its performance deteriorates. This results in increased operating cost, decreased productivity of the item and decrease in resale value of item.
- Sudden Failure: This type of failure occurs in equipment that do not deteriorate gradually with age but which fail suddenly after some period of service. The time period between installations and failure will not be constant for any particular equipment. However the failure pattern will follow certain frequency distribution that may be progressive, retrogressive or random in nature.
- Progressive failure: progressive failure occurs when probability of failure increases with the age of an item.
- Retrogressive failure: Certain items will have more probability of failure in the early years of their life and with the increase in the life of an item the chances of failure become less. That is, the ability of the item to survive in the initial years of life increases its expected life.
- Random failure: Random failure occurs when continuous probability of failure is related with equipment that fails because of random causes such as physical shocks that are independent of age. In the case of random failure, virtually all items fail before aging has any effect.
The replacement situations are categorized into the following four types:
- Replacement of capital equipment whose performance decreases with time.
- Group replacement items that fail completely: Some system usually composed of a large number of low cost items that are prone to failure with age such as failure of a resistor in television, radio, computer etc. In some cases the failure of a component may cause the complete failure of the system. In such cases, the cost of overall failure will be quite higher than the cost of component itself. In such situations, two types of replacement procedures must be considered. First is Individual replacement. In this policy, an item is replaced immediately after its failure. Secondly, Group replacement in which, decision is about the age when all the items should be replaced, irrespective of whether the items have failed or not. In this policy, the items that fail before the optimal time, will be replaced individually.
- Problem of mortality and staffing.
- Miscellaneous problems.
Replacement Planning Process:
- Assess clinical needs
- Use multidisciplinary approach
- Assess technical/maintenance/safety/regulatory needs/indicators
- Review equipment database
- Review maintenance criteria and calculations
- Assess budget
The current information used to make the decision to replace equipment includes equipment age, failures which cannot be repaired, current program needs, future strategic plans, and reliability assessments, if available. It is established that any equipment that cannot be repaired is typically replaced. This could be equipment that requires a complete deconstruction and rebuild, equipment that no longer has spare or replacement parts available, or the lack of a qualified and available technician.
Maintenance
Several management theorists focus on maintenance of equipment in manufacturing industry to sustain its position in marketplace. Theorists described maintenance as "a routine and recurring activity of keeping a particular machine or facility at its normal operating condition so that it can deliver its expected performance or service without causing any loss of time on account of accidental damage or breakdown". After designing, fabrication and installation of equipment, the operational availability of the same is looked after by the maintenance requirement. The concept of maintenance is used since earlier times and it was introduced along with origin of the machine. Previously, a machine was used as long as it worked. When it stopped working, it was either repaired, serviced or rejected. The high cost modern machines need to be properly maintained/serviced during their entire life cycle for maximizing their availability.Maintenance is significant organizational function that is needed to support production related processes. Breakdowns in production directly affects the output of the processes and thereby the productivity. The development of mechanization and automation of production systems and associated equipment, with the accompanying development of additional services and safety requirements, has made it compulsory for engineers to do proper maintenance of equipment. Fundamentally, maintenance is a function to retain the equipment or machine condition by replacing or repairing some of the components of the machine. According to Ben‐Daya and Duffuaa, "In general terms, equipment which is not well maintained and fails periodically experiences speed losses and/or lack of precision and, hence, tends to produce defects. More often than not such equipment drives manufacturing processes out of control. A process that is out of control produces defective products and therefore increases the production cost which amounts to less profitability which endangers the survival of the organization"(1995).
Relationship between Maintenance And Quality (Ben Daya and Duffuaa 1995)
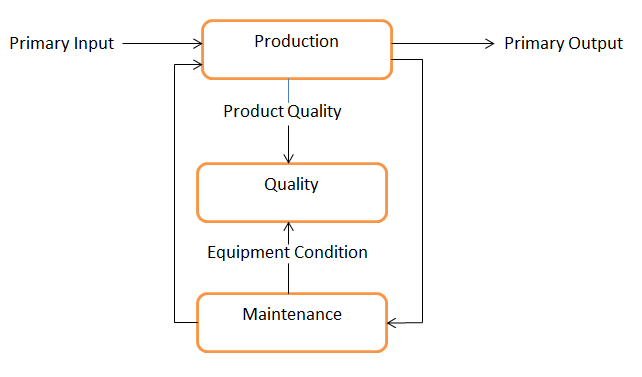
The maintenance theory is an outline plan of how the maintenance function will be performed. Based on the feedback obtained from the users and the history of the equipment, complete procedures are drawn to concretize the maintenance concept. The procedures developed are collectively called the maintenance plan. The growth of such a maintenance plan is requirements of the maintenance program that necessitates interaction between the operator and the manufacturer. With this information, the manufacturer can rearrange the design according to needs of users. Another feature of Maintenance function is to check safety measures of certain equipment where the failure of component may cause a major mishap.
Major steps in Maintenance
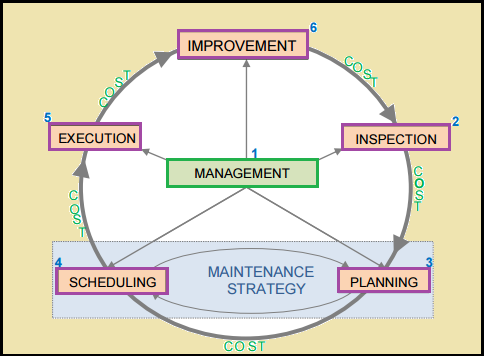
Objectives of maintenance: The objectives of maintenance must be devised within the framework of the overall organizational structure to accomplish major goals. The maintenance division must ensure that,
- The machinery and/or facilities are always in good working condition at the low cost.
- The time schedule to deliver the customers is not affected because of non-availability of machinery/service in working condition.
- The performance of the machinery or facility is dependable and reliable.
- The performance of the machinery or facility is kept to minimum to the event of the breakdown.
- The maintenance cost is well monitored to control overhead costs.
- The life of equipment is prolonged while maintaining the satisfactory level of performance to avoid needless replacements.
Types of maintenance systems:
Principally, maintenance can be classified into two groups:
- Breakdown maintenance
- Planned maintenance
Breakdown Maintenance:
In breakdown maintenance, no maintenance or repair work is done until a component or equipment fails or it cannot perform its normal performance. It is established that the maintenance work is called upon when the machine is not working and repairs are required to bring back the equipment to its original working condition. If the system is alone followed, it will lead to poor operational availability of the equipment, as spare parts may not be readily available. Breakdown maintenance describes the process flow which occurs when maintenance tasks are executed that usually precede a malfunction at technical object.Process flow (Source: Khan, 2013 )
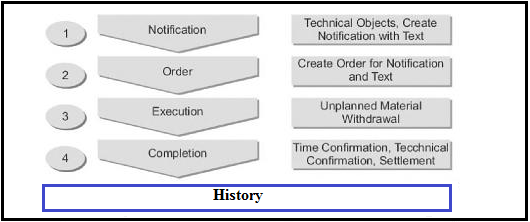
Though it appears to be cost-effective proposition, work would greatly suffer if the machine is not re-established to operational condition at the earliest. In this type of maintenance, during the repair time, it is not necessary to find out the cause of the breakdown, which in turn may lead to frequent failures of the same kind. Such practice is inexpensive for that machinery whose breakdown time and repair costs are less. But in case of high cost production systems, there are several limitations with breakdown maintenance.
Planned Maintenance
The planned maintenance is described as an organized type of maintenance. In this category of maintenance, the maintenance actions are planned well in advance in order to evade accidental failure. It will be pre-set not only the when and what kind of the maintenance work, but also by whom it would be undertaken. The requirements for planned maintenance include conduction of work study that decides the periodicity of maintenance work. Additionally, the conduction of Time Study assists in recommending ways and means of planning optimal maintenance schedules for the given system. In planned maintenance, instructions is given in detail and specific for each type of equipment. In the case, where safety is of utmost importance, the equipment condition should be checked every day. Therefore, the type of maintenance activity to be performed will depend upon the nature of equipment and its working conditions.The planned maintenance is classified into following types:
- Scheduled Maintenance (SM)
- Preventive Maintenance (PM)
- Corrective Maintenance (CM)
- Reliability Centred Maintenance (RCM)
Scheduled Maintenance
This type of maintenance activity is a stitch-in-time procedure to avoid break-downs. The actual maintenance program is planned in discussion with the production department, so that the appropriate equipment is made available for maintenance work. The frequency of such maintenance work is decided in advance from experience so as to utilize the idle time of the equipment efficiently. This also helps the maintenance department to use their manpower excellently. If the schedule of maintenance is known in advance, the specialists for the same can also be made available during the maintenance period. Scheduled maintenance is expensive as compared to breakdown maintenance, but the availability of equipment is enhanced. This practice is used for repairing of machines.Preventive Maintenance
It is also important category of planned maintenance. Preventive maintenance is planned and coordinated inspections, repairs, adjustments, and replacements which are carried out to minimize the problems of breakdown maintenance. Preventive maintenance is a basic maintenance system which is commonly applied in manufacturing environment in order to facilitate the production flow as well as enhancing the equipment productivity. Preventive maintenance usually relates to schedule with fixed time interval that is done daily, weekly, monthly or some other predetermined intervals. The use of performances interval is to implement preventive task when required. The planned activities involve the documented maintenances task, labour resources requirements, parts and material requirements, duration to perform task and also other technical references related to equipment. These actions are organized according to work's urgency, the work order, labour resource availability, duration to perform task as well as planning of parts and materials (Smith, 2004).Preventive maintenance has an important role in planning an operative maintenance schedule which can be combined with production scheduling, so that this will lead to the efficiency and effectiveness in manufacturing system. However, there are number of problems which occur during implementation of Preventive maintenance such as the overlapping between Preventive maintenance planning and production scheduling. The issue of integrating both areas is highlighted due to its importance in the competitive environment. Consequently, this will lead to the other problems that influence in operating system such as production flow, set up times cause downtime, increase the waste and the deterioration of equipment (Sortrakul, 2005). This practice encompasses planning and scheduling the maintenance work without disruption in production schedule and accordingly improves the availability of equipment. In preventive maintenance, a regular inspection of each item of equipment or at least the critical parts is done at fixed times to reveal the conditions that lead to production stoppage and harmful depreciation.
It is observed that planning and implementation of a preventive maintenance practice is expensive because it involves the replacement of all deteriorated parts/components during inspection. However, the higher cost of maintenance usually gets compensated by the long operational life of the equipment. This type of maintenance is generally used in complex plants to avoid serious breakdowns.
Corrective Maintenance
Corrective maintenance is used in repetitive failures of a certain part of the equipment. When such repetitive type of failures are observed, corrective maintenance can be applied in order to avoid reoccurrence of such failures. Corrective maintenance is explained as a dominant approach where equipment is allowed to run without interruptions and maintenance activities are conducted only when equipment fails. It requires minimum number of manpower and money spends to monitor the condition of equipment (Dhillon, 2006). However, the disadvantage of Corrective maintenance is high maintenance cost needed when any disastrous failure happen. These types of failures can be reported to the manufacturer to suggest amendments to the equipment. Main characteristics of a corrective maintenance program to restore an asset after failure has occurred.To manage the corrective maintenance, it is necessary to carrying out operations quickly, which allow the team be implemented in the shortest possible time, mean time to repair, low). Team must perform reliable operations, and adopting measures to prevent recurrence of these failure in a period of time long enough. They must use lowest amount of resources both labour and material.
Jonsson, 1997 stated that corrective maintenance and preventive maintenance at certain time intervals are the most common maintenance techniques.
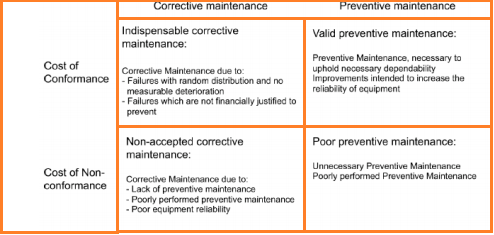
Reliability Centred Maintenance
This type of maintenance is used to recognise the maintenance requirements of equipment. The Reliability Centred Maintenance establishes the functional requirements and the desired performances standards of equipment and these are then related to design and integral reliability parameters of the machine. For each function, the associated functional failure is demarcated, and the failure modes and the consequences of the functional failures are analysed. The Goal of The Reliability Centred Maintenance is to achieve equipment reliability and availability by minimizing the probability of system failure. With this maintenance strategy, the function of the equipment is considered and possible failure modes and their consequences are recognised. Maintenance techniques that are cost-effective in minimizing the possibility of failure are then determined. The most operative techniques are adopted to improve the reliability of the facility. The consequences of each failure are recognised as one of the four categories: Hidden, safety or environmental, operational, and no operational. Following the Reliability Centred Maintenance logic, preventive maintenance tasks which will avert these consequences are selected, provided the applicability and effectiveness criteria for preventive maintenance are satisfied.The applicability requirements denote to the technical features and efficiency criteria for preventive maintenance tasks and the frequency at which these should be done. Effectiveness criteria depend on the consequences of the failure; probabilities of the multiple failures for hidden failure consequences, acceptable low risk of failure for safety consequences, and non-operational consequences.
The drawback of this type of maintenance is that The Reliability Centred Maintenance does not readily consider the total cost of owning and maintaining an asset. Additional costs of ownership, like those considered in Evidence Based Maintenance, are not considered, and are therefore not factored into the maintenance considerations.
Planned maintenance in top companies
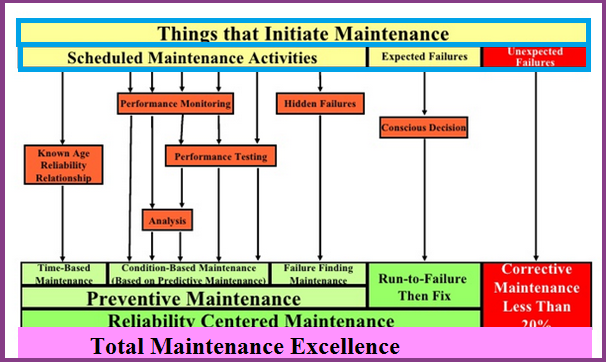
Benefits of maintenance: In production system, manufacturers have to invest in huge amount of funds and in return they expect good value from the equipment. To get optimal results, regular maintenance is required. Effective maintenance system has following benefits:
- The minimization of breakdown time
- Improvement in total availability of the system with their optimum capacity
- Extended useful life of the equipment
- Safety of the personnel
Challenges faced by organization in maintaining equipment:
The maintenance function of contemporary industry faces numerous challenges which include:
- Rapid growth of technology resulting in current technology becoming obsolete. Such a challenge is a frequent one in Information and Communications Technology industry where computers and computers based system (hardware and Software) are the main components.
- Initiation of new advanced diagnostic tools, rapid repair systems.
- Advance store management methods to integrate modular technologies.
- Requirements of retaining both out-of-date and modern machines in service.
The effective management of maintenance aspects under such challenging circumstances is often a difficult job. Besides the rectification of the faults in the equipment, the activities of the maintenance department include up gradation of the existing plants and equipment and training of maintenance personnel to attain the required technical skills, operative maintenance of the old equipment for higher availability, cost optimization of all maintenance functions, improvement of maintenance activities in the areas of tribology, reconditioning of used /unserviceable spare parts, development of indigenous sources for parts as import substitution, setting up of an effective maintenance information management systems, effective utilization of the maintenance workforce and establishing in house R&D activities for effecting improvements in maintenance practices.
It can be analysed that maintenance is effective way to maintain and improve the quality of the elements involved in a production process, constantly and cost-effectively through identifying and controlling the deviations in the condition of a production process that is decided by production costs, and working environment. The main aim of regular maintenance is to make sure that all equipment required for production is operating at 100% efficiency at all times.