Flexible Systems Management (Managerial Function)
Flexibility is a type of characteristics in management that facilitates a mixed model manufacturing system to cope up with a certain level of variations in part or product style, without having any interruption in production due to changeovers between models. Flexibility measures the capacity to adjust to range of possible environment. In order to become flexible, a manufacturing system must possess some capabilities that include Identification of the different production units to perform the correct operation and quick changeover of operating instructions to the computer controlled production machines. Flexible manufacturing system is developed in order to gain competitive advantage in tough business environment.
A flexible manufacturing system is a manufacturing system in which there is some extent of flexibility that permits the system to react when there are changes in environment, whether predicted or unpredicted. The notion of Flexible manufacturing systems is explained as the most automated and technologically sophisticated of the machine cell types used to implement cellular manufacturing. This system has multiple automated stations and is capable of variable routings among stations, while its flexibility allows it to operate as a mixed model system. The term flexible manufacturing systems emerged in the decade of 1960s when robots, programmable controllers, and computerized numerical controls brought a controlled setting to the factory floor in the form of numerically-controlled and direct-numerically-controlled machines. In many part, flexible manufacturing system is restricted to firms involved in batch production or job shop environments, such as lathes, milling machines, or drill, presses, are all costly and may not reach to full capacity. Flexible manufacturing systems offer the batch manufacturer with another option that can make batch manufacturing just as competent and productive as mass production.
This flexibility has two categories. The first category, machine flexibility include the system's capacity to be changed to produce new product types, and ability to change the order of operations executed on a part. The second category is termed as routing flexibility, which comprises of the ability to use multiple machines to perform the same operation on a part, as well as the system's ability to absorb large-scale changes, such as in volume, capacity, or capability. Routing flexibility can be vital to deal with different kinds of volume demands for different part variants and to maintain through-put capabilities in terms of machine breakdowns. The FMS concept integrates many of the advanced technologies including flexible automation. Most flexible manufacturing system consist of three main systems. The work machines which are often automated CNC machines are connected by a material handling system to optimize parts flow and the central control computer which controls material movements and machine flow. Flexible manufacturing system is a group of manufacturing cells linked by an automatic material handling system and a central computer. It manufactures a mix of piece-part types while being flexible enough to consecutively manufacture different piece-part type mixes without costly, time-consuming, changeover requirement. It is a medium size batch production system.
Flexible Manufacturing System
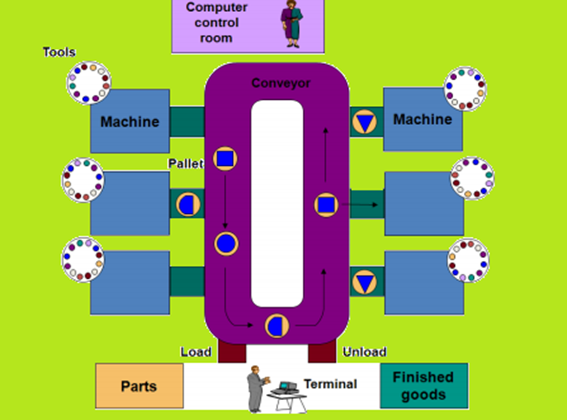
Basic components of Flexible manufacturing system as follows:
Workstations: These are basically CNC tools that performs machining process on various parts.
Automated material handling and storage system: They are used to transport work parts between the processing stations, sometimes integrating storage into function.
Computer control system: It is used to synchronize the processing stations and material handling in Flexible manufacturing system.
Flexible manufacturing system can be differentiated by the manner they perform, as either processing operations or assembly operations. Flexible manufacturing system are custom-built so that company can find a comprehensive range of system that have been implemented to differing projects. Each Flexible manufacturing system is customized and exclusive. Flexible manufacturing system is basically, the number of machines it contains; or whether it is a dedicated or random-order FMS, in terms of the parts it processes.
There are different types of flexibility that are showed by manufacturing systems:
- Machine Flexibility. It is the ability to adjust a given machine in the system to a wide range of production operations and part styles. The greater the range of operations and part styles of the machine, greater will be the machine flexibility. The various factors on which machine flexibility depends are setup or changeover time, ease with which part-programs can be downloaded to machines, tool storage capacity of machines, and skill and versatility of workers in the systems.
- Production Flexibility. It is the range of part styles that can be produced on the systems. The range of part styles that can be produced by a manufacturing system at reasonable cost and time is determined by the process envelope. It depends on many factors that include machine flexibility of individual stations, range of machine flexibilities of all stations in the system.
- Mix Flexibility. It is explained as the facility to change the product mix while maintaining the same total production quantity that is, producing the same parts only in different proportions. It is also known as process flexibility. Mix flexibility gives protection against market changeability by accommodating changes in product mix due to the use of shared resources. However, high mix variations may result in requirements for a greater number of tools, fixtures, and other resources. Mixed flexibility depends on factors such as similarity of parts in the mix, machine flexibility, and relative work content times of parts produced.
- Product Flexibility. It is an ability to change over to a new set of products economically and rapidly in response to the varying market requirements. The change over time includes the time for designing, planning, tooling, and fixturing of new products introduced in the manufacturing line-up. Product Flexibility depends upon factors like relatedness of new part design with the existing part family. Off-line part program preparation and machine flexibility
- Routing Flexibility. It is described as ability to produce parts on alternative workstation in case of equipment breakdowns, tool failure, and other disruptions at any particular station. It helps in increasing output, in the presence of exterior changes such as product mix, engineering changes, or new product introductions. Factors which decides routing flexibility include similarity of parts in the mix, similarity of workstations, and common tooling.
- Volume Flexibility. It is the capacity of the system to vary the production volumes of different products to accommodate changes in demand while remaining lucrative. It can also be referred as capacity flexibility. Factors that impact the volume flexibility are level of manual labor performing production, amount invested in capital equipment,
- Expansion Flexibility. It is described as the ease with which the system can be expanded to raise total production volume. Expansion flexibility depends on several factors that include cost incurred in adding new workstations and trained workers, easiness in expansion of layout, type of part handling system used.
Flexible manufacturing system guarantees quality product at minimum rate while maintaining small lead-time. Therefore companies adopt Flexible manufacturing system to fulfill growing requirements of customized production. Major objectives of Flexible manufacturing system is to accomplish efficiency of well-balanced transfer line while retaining the flexibility of the job shop (Stecke, 1985). A flexible manufacturing system has four or more processing workstations connected mechanically by a common part handling system and electronically by a distributed computer system. It includes a wide range of manufacturing operations like machining, sheet metal working, welding, fabricating, scheduling and assembly. Using Flexible manufacturing system, companies can produce variety of products without making any changes in the hardware set-up. Consequently, the changeover time between two products can be reduced to the time required by the machine tools to receive the necessary instructions. It also reduces the lead-time drastically.
Various types of flexible manufacturing system include Sequential FMS, Random FMS, Dedicated FMS, Engineered FMS and Modular FMS. Sequential FMS manufactures one-piece part batch type and then planning and preparation is done for the next piece part batch type to be manufactured. It operates like a small batch flexible transfer line. Random FMS manufactures any random mix of piece part types at any one time. Dedicated FMS constantly manufactures, for lengthy periods, the same but limited mix of piece part batch types. Engineered FMS manufactures the same mix of part types throughout its lifetime. Modular FMS enables user to expand their FMS capabilities in a stepwise fashion into any of the earlier four types of FMS.
Developing a flexible manufacturing system:
A company that intend to develop an effective flexible manufacturing system has five major stages of development that include Awareness phase, Planning phase, Procurement phase, Installation phase and Operation phase.
Figure: Phases of the development of F.M.S
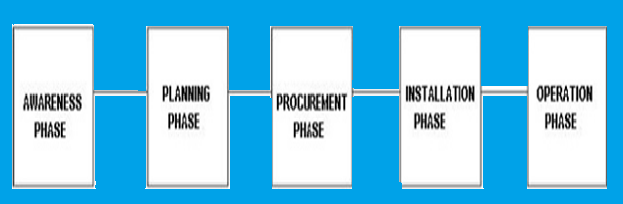
Awareness Phase: In this phase, company has to collect all the information it needs to understand the model of flexible manufacturing system and the potential it holds for the company. It must check whether the flexible manufacturing system suits the company's job profile and weather it can derive any significant benefits from it.
Planning Phase: Once the company decides to go forward through flexible manufacturing system planning an F.M.S., which suits its requirements, the first step in this direction would be the setting up of a project team with a project leader to supervise the whole project. The team should perform a financial evaluation of the company before taking any further steps towards the development of the F.M.S. On the basis of evaluation report, the team should articulate a long-term strategy for the effective utilization of the flexible manufacturing system. The team should then select as to which machining processes it must embrace in its F.M.S. to accomplish the job requirement. The F.M.S. that the company develops should be modular in nature, as it would allow the company to add new modules. At the end of the planning phase the team comes out with a concrete set of specifications to go to the procurement phase.
Procurement Phase: The procurement team is assigned with the job of buying all the hardware and software components required for setting up the flexible manufacturing system in the company. For this it selects appropriate suppliers based on certain criteria.
Installation Phase: Once all the components are procured they need to be suitably installed and integrated to form the flexible manufacturing system. To do this, it is vital that the various suppliers and the F.M.S. user be present to sort out any problems that may arise during the integration process. The harmonized efforts from all the parties involved will guarantee a comparatively smooth installation of the flexible manufacturing system. The installation phase involves various tasks that include construction of the F.M.S. site, establishing of the hardware and software components of the system, Integration of components to form the F.M.S., Integration of the other departments to the F.M.S, Planning the test and acceptance methods suitable to all parties and Planning for the training and take-over activities.
Operation Phase: After installation of the F.M.S., operation process begin. During the initial process, errors are likely to appear in the hardware and software. These errors have to be debugged for the smooth operation of the system. With time, flexible manufacturing system, user learns to comprehend the system according to his needs.
The benefits of flexible manufacturing system is its high flexibility in managing manufacturing resources like time and effort in order to manufacture a new product. The best use of flexible manufacturing system is in the production of small products like those from a mass production. Other advantages are Lower cost per unit produced, greater labor productivity, greater machine efficiency, and improved quality, increased system reliability, and reduced parts inventories, adaptability to CAD/CAM operations and shorter lead times. Major drawbacks are Cost to implement, Substantial pre-planning, Requirement of skilled labor and Complicated system. Tactical advantage of flexible manufacturing system is that it is able to tackle the risk caused by ambiguity about the future. It can be done through planning in a way that maintains flexibility of the environment. Although it is difficult to predict the future, one can make estimates of probabilities and proceed in ways to accord with the future.
To sum up, Flexible manufacturing system is highly automated GT machine cell that comprises of group of processing station. Interconnected by automated material handling and storage system and controlled by integrating computer system. It is a flexible system because it is capable of processing numerous different parts style simultaneously at various work station. Flexible manufacturing system is proficient to accommodate engineering and process changes that are responsible to occur during manufacturing. FMS provides flexibility to deal with varied part and product designs, and allows variation in parts' processing sequences and production volume changes. Its efficacious implementation results in improvement of capital utilization, higher profit margins, and increased competitiveness.