Fundamentals of Operations Management
Operation is important part of any business firm. Operations management focuses on managing the sources directly taking share in product manufacturing or providing a service by the organization, achieving the strategic goals of the organizations. Sources are usually characterized by people, materials, technologies and information. They are pooled together by a number of processes in order to be used for acquiring an organization primary service or a product. Operations management can be understood as a transformation development in which inputs (resources) are by means of this process transformed into outputs (products or services). Refer to below figure:
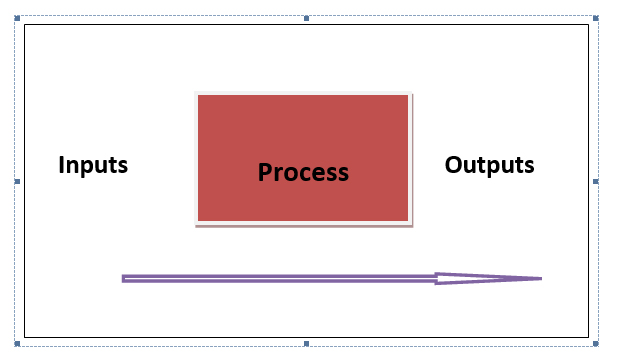
Historical Review
Since many centuries, operations management has been recognized as a significant factor in any country's economic development. The conventional view of manufacturing management began in eighteenth century when Adam Smith recognised the economic benefits of specialization of labour. He suggested breaking of jobs down into subtasks and recognises workers to specialized tasks in which they would become highly skilled and efficient. In the early twentieth century, F.W. Taylor implemented Smith's theories and developed scientific management. From then till 1930, many techniques were developed including existing traditional view.
Basic concept of operation management:
Operations management are the activities, decisions & responsibilities of managing the production and delivery of products and/or services"(Slack et al, 2007:4). Other theorists defined it as the management of the processes that produce or deliver goods and/or services"(Greasley, 2009:3). Operation managers are involved in planning, organizing, and controlling the activities which affect human behaviour through models. It can be elaborated in detail.
Planning
Activities that establishes a course of action and guide future decision-making is planning. The operations manager defines the objectives for the operations subsystem of the organization, and the policies, and procedures for achieving the objectives. This stage includes clarifying the role and focus of operations in the organization's overall strategy. It also involves product planning, facility designing and using the conversion process.
Organizing
Activities that establishes a structure of tasks and authority. Operation managers establish a structure of roles and the flow of information within the operations subsystem. They determine the activities required to achieve the goals and assign authority and responsibility for carrying them out.
Controlling
Activities that assure the actual performance in accordance with planned performance. To ensure that the plans for the operations subsystems are accomplished, the operations manager must exercise control by measuring actual outputs and comparing them to planned operations management. Controlling costs, quality, and schedules are the important functions here.
Behaviour
Operation managers are concerned with how their efforts to plan, organize, and control affect human behaviour. They also want to know how the behaviour of subordinates can affect management's planning, organizing, and controlling actions. Their interest lies in decision-making behaviour.
Models
As operation managers plan, organise, and control the conversion process, they encounter many problems and must make many decisions. They can simplify their difficulties using models like aggregate planning models for examining how best to use existing capacity in short-term, break even analysis to identify break even volumes, linear programming and computer simulation for capacity utilisation, decision tree analysis for long-term capacity problem of facility expansion, simple median model for determining best locations of facilities etc.
Below figure shows the general model of operation management: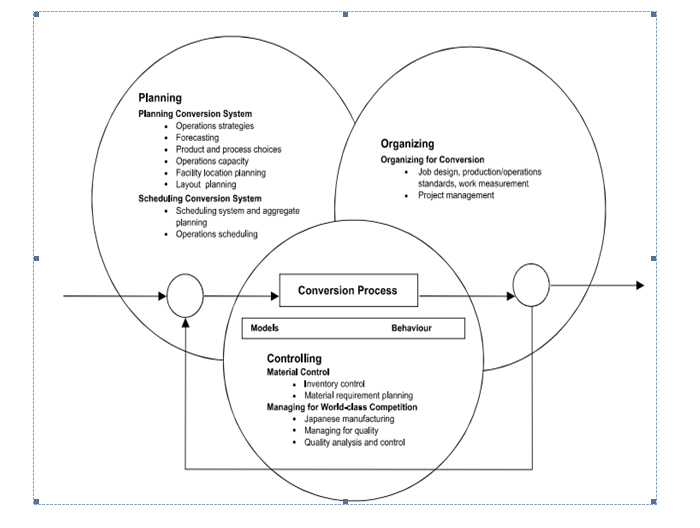
Role of Operation Managers
operations managers are responsible to take major decisions about product development, process and layout decisions, site location, and capacity. At the tactical level, operations management addresses the issues relevant to efficiently scheduling material and labour within the constraints of the firm's strategy and making aggregate planning decisions. Operations managers have a hand in deciding employee levels, inventory levels and capacity. At the operational level, operations management is concerned with lower-level planning and control. Operations managers and their subordinates must make decisions regarding scheduling, sequencing, loading, and work assignments. Presently, operations manager must have knowledge of advanced operations technology and technical knowledge relevant to his/her industry, as well as interpersonal skills and knowledge of other functional areas within the firm. Operations managers must also have the ability to communicate effectively, to motivate other people, manage projects, and work on multidisciplinary teams.
Goal of Operation Management
Major objective of operations management is to provide good customer service and resource utilisation. The operating system must provide something to a specification which can satisfy the customer in terms of cost and timing. Thus, primary objective can be satisfied by providing the 'right thing at a right price at the right time.
Below table elaborate the aspects of customer service: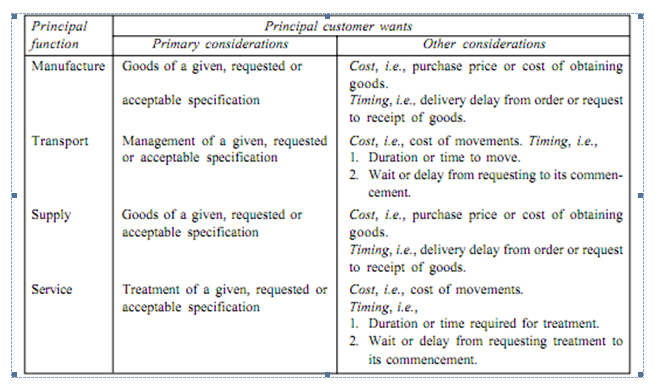
Other key goal is best utilization of resources to satisfy customers. Operations management is concerned basically with the utilisation of resources, i.e. obtaining maximum effect from resources or minimising their loss, under utilisation or waste. The extent of the utilisation of the resources' potential might be expressed in terms of the proportion of available time used or occupied, space utilisation, levels of activity, etc. Each measure indicates the extent to which the potential or capacity of such resources is utilised. This is referred as the objective of resource utilisation.
Methods of Operation Management
Operations managers deal with two basic fields of activities. The first range of tasks to be solved is a design of operations system, the second one is then planning and control of operations (Dilworth, 1992). Design of operations system includes huge number of tasks. One of the very important decisions that are part of organization's strategy and whose wrong implementation can influence its competitiveness, costs, sales and profit, and decision on facility location for manufacturing or services. Factors influencing the decision on facility location are of three types. The consequent task in the field of operations system design is a decision on facility layout and operation process layout. Different operations, various conditions and objectives call for alternative ways of process layout.
It can be summarised that operation is a process by which goods and services are developed. It deals with decision making related to productive process to ensure that the resulting goods and services are produced according to specifications, in the amount and by the schedule it required and at minimum cost. Theoretical studies explain that operational management start with business plans and strategies which are based on the demands for product and services.