Job and Process Costing
In accounting, there are two basic systems used to assign costs to products or services that include Job costing and process costing.
Job costing: Job costing is dominant mechanism to trace specific costs to individual jobs and investigate them to check if the costs can be decreased in later jobs. In job costing, an individual unit, batch, or lot of a distinct job product or service called a job. Job costing entails a series of transactions that collect the cost of materials, labour, and overhead to a particular job. It is used to accumulate costs at a small-unit level. For instance, job costing is suitable to derive the cost of developing a software program, building construction, or manufacturing small products. It is said by experts that job costing is most suited for construction companies that execute work based on contracts and manufacturing operations that produce goods in batches based on a specific job order. The costs of each contract or production order are easily assigned to the units being produced whether they are houses or plastic products. Job Costing is used in that industry where employer distinguishes one job with other job. In that situation, they can collect cost of each work order or product line.
Major objectives of job costing are to ascertain the cost of production every year, to determine the profitability of each job in order to undertake future order of similar nature, to control operational efficiency by comparing actual cost with estimated cost and to plan future course of activities (Rajasekaran V., 2010).
Job costing involves the following accounting activities:
Materials: It collects the cost of parts and then assigns these costs to a product or project once the components are used.
Labour: Workers charge their time to particular jobs, which are then assigned to the jobs based on the labour cost of the employees.
Overhead: It accumulates overhead costs in cost pools, and then allocates these costs to jobs.
Features of the Job Costing:
The Job Costing System checks all costs associated with jobs done by the company.
Each job in the Job Costing System is given a unique number that identifies the job.
Each job can be subdivided into any number of activities used to track costs of individual tasks within a job. Each of these activities refers to a general ledger account number where the costs are to be accumulated.
Each activity contains costs to date for that activity along with budget estimates.
Job cost reports can be used to compare the actual expenditures against the budgeted amounts to watch the progress of a job.
All of the Accounting System modules can charge costs to an activity of a job.
Payroll costs can be charged against an activity through the Payroll System.
Direct purchases are charged against an activity.
It is also probable to charge the cost of inventory items used against an activity.
The Job Costing System relocates the costs of a job to a work in process account while the job is in progress, and transfers those costs to the proper expense accounts when the job is finished.
A job may be produced using existing jobs as a model.
Numerous job cost reports are available which give various levels of detail. The reports range from giving one total per existing job to detailing every single transaction that has been made against each job.
Common Approach to Job Costing
Seven step approaches is used to assign actual cost to individual jobs:
- Identify the chosen cost object(s).
- Identify the direct costs of the job.
- Select the cost allocation base(s).
- Identify the indirect costs associated with each cost-allocation base.
- Compute the rate per unit of each cost-allocation base used to allocate indirect costs to the job.
- Compute the indirect costs allocated to the job.
- Compute the cost of the job by adding all direct and indirect costs assigned to it.
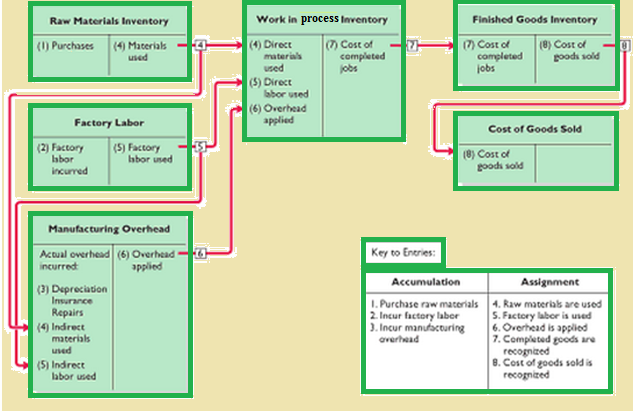
Merits and Demerits of Job Costing
Major benefits of job costing system are that the management team has easy access to all the costs incurred for each job being finished. This enables the team to scrutinize each cost incurred, explore the reason for this happening and find out how it can be controlled better in the future, thus contributing to better ongoing levels of profitability. Another benefit of job order costing system is that it yields ongoing results for each job. In computerized production tracking data bases, experts can use a job costing system to track costs as they are added. This offers benefits to the company such as the accounting staff can observe job accounts to see if costs are being posted to the wrong accounts and correct them immediately instead of waiting until the job closes. Another advantage is that a company can monitor the costs incurred for longer jobs and have sufficient time to make changes before they lock, based on the costing information revealed by the job costing system.
Drawbacks of adopting job costing system are that overhead is usually allocated based on rates that are changed only about once a year. Substantial variation in overhead costs over the course of a year can result both in over and under allocation of overhead costs to jobs during that period. Other issue associated with job costing system is that it is specific to the use of normal costing. This practice involves the use of standard overhead rate rather than one that is based on actual costs and requires adjustment from time to time. Job costing has little application in some environments. For example, the software industries have high development costs but almost zero direct costs linked with the sale of its products. The use of a job order costing system to record these costs makes little sense if the associated costs symbolize only a few percent of the total income generated from each one. Job costing involves lots of clerical work and management cannot find precisely the operating efficiency of men and machine.
Process Costing: Process Costing is a procedure to find out the cost of product in each process. In process costing, the cost object is masses of identical units of the products or services. It allocates costs among all the products manufactured during that time. It is used by manufacturers to calculate the cost of per unit for product. Process costing is a method of costing used mainly in manufacturing where units are constantly mass-produced through one or more processes. It is type of operational costing and used in various industries such as textile, chemical rubber, steel, sugar, shoes, and petrol.
The main purpose of process costing is to control the process, to know cumulative cost, to calculate the value of inventory of raw material, work in progress, and finished goods at the end of period. This method is also used to assign the price of the products.
Theoretical studies revealed that process costing is the costing method applicable where goods and services result from a sequence of continuous operations. Costs are arranged over the unit produced during the period (Rajasekaran V., 2010). In process costing, the process calculated. The method used is to take the total cost of the process and average it over the units of production.
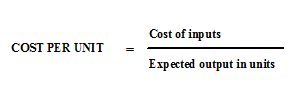
Features of Process Costing
The production is constant and cost flow from one process to another.
The production is homogenous and standardized. They are not distinguishable in processing stage.
Outcome of one process become raw material for another process.
Costs are collected process wise. The cost of normal wastage is included in the cost of total unit produced.
The total cost of each process is divided by the normal output of that process to find out cost per unit of that process.
The units which are incomplete at each stage of production are converted into equivalent production based on the degree of incompleteness.
At the end of the accounting period, there will be stock of semi-finished goods or WIP (Work in progress). The reason is due to the continuous nature of manufacturing process. Therefore, apportionment process cost has to be made between the finished product and WIP at the end of each accounting period (Rajasekaran V., 2010).
process cost flow (Source: Weygandt, 2009 )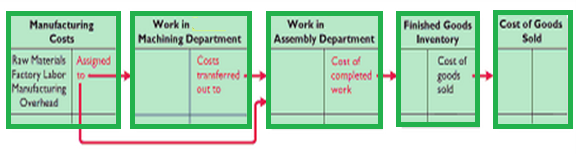
Basic advantages of process costing: In process costing, there is periodical determination of cost. This procedure is simple and cheap. There is a managerial control over this process.
Limitations of cost processing: This method do not analyse in details and it is difficult to calculate average cost where more than one product is produced.
Methods of process costing: There are some methods by which process costing is done.
Fifo method: This method follows the principle that materials used should carry the actual experienced cost of the specific unit used. It is accurate but more complex. It is applicable where size and cost is large.
Weighted average method: It presumes that all costs whether from previous period or current one lumped together and assigned to produce units. In this method, calculation is simple and used where assigning a particular cost to an individual unit is impossible.
Job and Process Costing Systems has similar characteristics:
Both type of costing have similar fundamental aim that is to assign material, labour, and overhead cost to products.
Job and process costing systems use the same indispensable manufacturing accounts: Manufacturing Overhead, Raw Materials, Work In Process, and Finished Goods.
The flow of costs through the manufacturing accounts is principally the identical.
Both costing system debit raw material to raw material inventory, factory labour to factory labour and manufacturing overhead cost to manufacturing overhead.
Differences between Job And Process Costing System
The job costing system uses only one work in process account whereas process costing uses multiple works. Job costing charge to individual cost and summarizes them in job cost sheet. Process costing summarizes cost in production cost report for each department. Job costing totals cost after completion of job whereas process costing totals cost at the end of the period ( Weygandt, 2009).
The difference between Job and process costing systems ( Source: Rajasekaran V., 2010)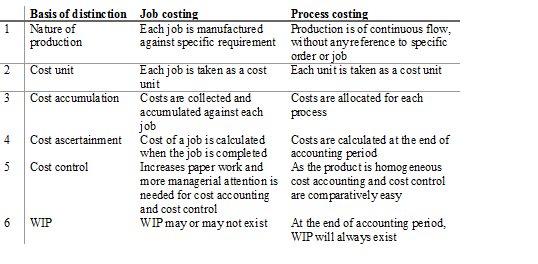
It can be said that both processes have similarities and differences. In job costing, company assign costs to each job whereas in process costing company track cost through the series of connected manufacturing process instead of individual job.
Analysis of similarity and differences between job and process costing (Source: Source: Weygandt, 2009).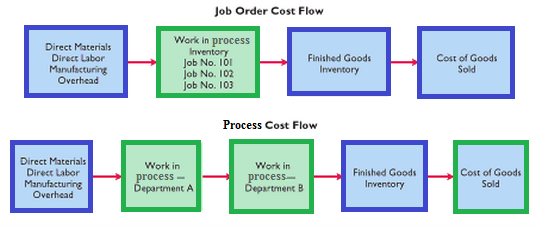
To summarize, process costing is one of the significant procedure of costing applied in industries where manufacturing of products involve several operations or different stages of production. Companies use process costing systems to apply costs to similar products that are produced at large scale and in continual fashion. Job costing estimates cost of different jobs in manufacturing products per specific consumer order. Basically, Job costing is a product costing system that amasses and assigns costs to a specific job. Process costing accumulates product or service costs by process or department and then assigns them to a large number of nearly alike products.