Role and Importance of Materials Management
Materials management is principally associated with the acquisition, control and use of materials needed and flow of goods and services connected with the production process having some predetermined objectives in view.
Concept of material management:
Materials Management is merely the process by which firms are supplied with the goods and services that it needs to accomplish its objectives of buying, storage and movement of materials. Materials Management has different functions that include planning, procuring, storing and providing the suitable material of precise quality, right quantity at right place in right time in order to organize and plan the production activity in an integrative manner for business undertaking. According to management theorists, materials management is total conception of having its definite organization to plan and control materials, its supply, and its flow from raw stage to finished stage so as to deliver the product to customers as per their requirements in time. This entails materials planning, purchasing, receiving, storing, inventory control, scheduling, production, physical distribution and marketing. It also controls the materials handling and its interchange. The materials manager has to deal with these functions with suitable authority and accountability in the material management. Tersine and Campbell (2004) define material management as the process to provide the right materials at the right place at the right time in order to maintain a desired level of production at minimum cost. The purpose of material management is to control the flow of materials effectively. Another theorist, Ammer, Dean (1991) defines material management as the process in which a company acquires the materials that it needs to achieve their objectives. This process usually begins with the requisition of materials from the supplier until the material is used or incorporated into a product. There is a need for material management in organization. The incorporation of the functions related to materials into a single department makes it easier to control and identify all the activities related to material flow and costs.
Historical Review
During World War-I, there were insufficiency of materials in USA to a huge scale and production managers were unable to manage supply the War goods. This led to organize the Materials Management department for managing large inventories in stores and to investigate the problems emerged to control and cut down inventory cost problems and scarcity removal. Since then, the materials management was considered as a vital function of the management. With the development of standards of scientific management by F.W. Taylor in 20th century, the economic use of materials in all firms was decisively felt to lessen the cost of production. In early phase, materials purchase and supply systematically begins from 1850. Charles Baggage's write-ups in 1832 refer to the significance of purchasing function. Baggage is also recognized as "Materials Man". Purchasing gained significance during World War I. Howard T. Lewis was a purchasing professional from 1905 to 1945. He developed importance of sound procurement to company operation. The idea of materials management was extensively spread during World War II. Professor Howard T. Lewis of the Harvard Business School made the wide-ranging studies in Industrial Purchasing Practice. W.N. Michelle, N.F. Harriman, L.F. Buffy, Donald G. Clark, Edward T. Gushee, Russell Forbes, Stuart F. Hewritz and George A. Reward had great role to purchasing and materials management in procuring, receiving, inventory control and supply. World War II introduced a new period in purchasing history. In 1933, nine colleges offered courses in purchasing which was increased to forty-nine colleges in 1945 in America. The post-war period visualized the expansion of the value analysis technique which was originated by General Electric Company in 1947 on the assessment of which materials or changes in the specification and design would reduce overall product cost. During the period of 1947 to 1960 there were huge developments in materials management. The Vietnam War resulted in rising price and materials availability pressure. During 1970, organizations realized extensive materials problems related to 'oil shortages and embargoes'. Common agreement between countries were made with the general objective to solve materials issues including materials planning, inventory control, purchasing, quality control, stores control, materials movement and surplus disposal. The purchasing policies and behaviours that evolved over in 1980 gave rise to international competition. In international business in between 1970 and 1999, materials management concept was expanded. After 2000, purchasing approaches reveal a changing prominence towards the upgrading of quality of materials, supplier relationship, more co-operative approach, long-term strategies of cost management and database materials management systems for materials planning and utilization in industries to bring about overall improvement in production systems, in-cost reduction through economy and increased sales.
Major Objectives of Material Management
The main objectives of materials management are to reduce material cost, to purchase, receive, transport and store materials efficiently and to reduce the related cost, to cut down costs through simplification, standardisation, value analysis, import substitution, to trace new sources of supply and to develop cordial relations with them in order to ensure continuous supply at reasonable rates, to reduce investment tied in the inventories for use in other productive purposes and to develop high inventory turnover ratios. Basically, objectives of material management are classified into primary and secondary objectives. Primary objectives include efficient materials planning, buying or Purchasing, procuring and receiving, storing and inventory control, supply and distribution of materials, quality assurance, good supplier and customer relationship and improved departmental efficiency. General secondary objectives of material management are efficient production scheduling, to take or buy decisions, prepare specifications and standardisation of materials, to assist in product design and development, forecasting demand and quantity of materials requirements, quality control of materials purchased, material handling, use of value analysis and value engineering, developing skills of workers in materials management and smooth flow of materials in and out of the organization.
There are numerous functions of material management. The basic function to accomplish primary objectives is materials requirements planning which is essential operation in multinational companies. The advance technique of "Just in Time" is used which has no inventory. Another function of material management is purchasing which has to be performed successfully with its suppliers. The success depends on the competence by which this particular function of purchasing and procuring the requisite materials at appropriate time will be done and its availability is assured. In order to get success in purchasing function, organizations must consider that the requisition of material is needed by proper authority to initiate its purchase. It is important to select appropriate supplier for the materials requisitioned, before placing an order. Company must negotiate about the price of the material from the supplier and it will be purchased at the cheapest price. The quality of material must be assured and should not be compromised with the cost of the material. The material should be purchased of right quantity and right quality at proper time at the cheapest cost. It is recommended to set the proper purchase policy and procedure. Other function of material management is inventory planning and control which explains that the materials should be purchased and brought in the stores just before it enters the production or sold out so that inventory cost is negligible. The zero inventories are the perfect planning. There are three types of inventories such as raw materials, purchased goods and finished parts and components (Figure: 1).
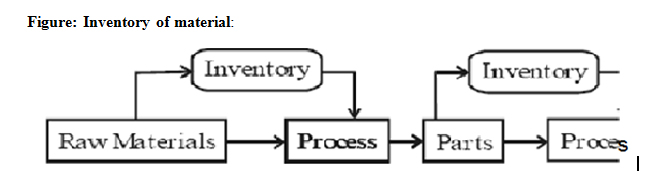
Inventory at different levels is required to confirm about the availability of all these types of materials and goods and their proper flow from one facility to another at different levels of production centres in a manufacturing concern. The storing of various types of materials and parts as inventory is highly significant before it is delivered to end users and use at different production centres. This involves inventory planning and control of materials in the stores department. Next primary function of material management is ascertaining and maintaining the flow and supply of materials which must be maintained by the materials management subdivision. Inadequate or zero inventories may develop the situations of stock-outs and impact in production. Stoppage of materials handling devices is also responsible for trouble of material supplies. Other important primary function of material management is quality control of materials which is important to buy the right quality of materials. The standard dimensions like the inspection, quality control, simplification, specification, and standardization must be considered for the measurement of quality of the materials. Quality is basically governed by choices of customers and the market is under buyer's control. Material quality control intends to deliver product at superior quality at affordable price. The product will be specified by its quality standards, durability and dependability, high performance, reliability and visual value. Lastly, departmental efficiency is the primary function of quality management which ensures the efficiency of the system adopted. In order to uphold the things in appropriate way as per planning, an efficient control is necessary in the department over each and every process. Management Information System and feedback control at every stage of working must be implemented to control and make the management and employee work as efficiently as possible to achieve the best results.
There are many secondary functions of material management which adds value to customers. The first function is standardization and simplification which are set by design and technical department of the organization and they are followed by production department. Standards describe the quality, reduction in sizes and variety, interchangeably of parts and products. It makes certain efficient utilization of materials and reduces wastages. Another secondary function is design and development of the product which is significant to promote sale. The new techniques of designing a product using Computer Aided Design has contributed to develop variety of products at rapid rate. Next function is Make and buy decisions which are the policy decisions of the management. The capacity of the organization and the various facility developed by the organization to produce various items is the main purpose of every organization. The make and buy decisions are based on cost economics and cost benefit analysis made by the organization using the existing production capacity of labour, skill and machines available with the factory and how best they can be utilized. Another function of materials management is Coding and Classification of Materials which assist the production and purchasing department of every organization. The materials are recognized to purchase and store as an inventory by its codes and nomenclatures. Next function is forecasting and planning. Numerous methods of forecasting are available and the materials management department can choose the one which gives the best results to the company.
Advantages of Material Management
Effectual material management system can bring numerous advantages for organization in competitive business such as reducing the overall costs of materials, better handling of materials, reduction in duplicated orders, materials will be on site when needed and in the quantities required, improvements in labour productivity, improvements in project schedule, quality control, better field material control, better relations with suppliers, reduce of materials surplus, reduce storage of materials on site, labour savings, stock reduction, purchase savings and better cash flow management.
To sum up, materials management thought is to deal with resources in an integrative way for national fiscal development. It is a conceptual frame for thoroughly addressing the movement of materials through the economy and the environment from extraction to end point.