Process Planning
In companies, planning processes can result in increased output, higher precision, and faster turnaround for vital business tasks. A process is described as a set of steps that result in a specific outcome. It converts input into output. Process planning is also called manufacturing planning, material processing, process engineering, and machine routing. It is the act of preparing detailed work instructions to produce a part. It is a complete description of specific stages in the production process. Process planning determines how the product will be produced or service will be provided. Process planning converts design information into the process steps and instructions to powerfully and effectively manufacture products. As the design process is supported by many computer-aided tools, computer-aided process planning (CAPP) has evolved to make simpler and improve process planning and realize more effectual use of manufacturing resources.
Process Planning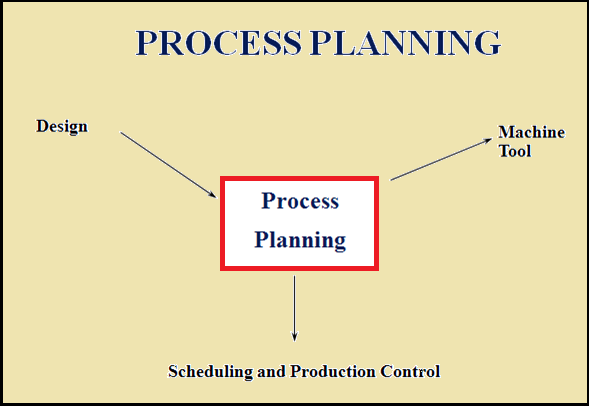
It has been documented that process planning is required for new product and services. It is the base for designing factory buildings, facility layout and selecting production equipment. It also affects the job design and quality control.
Objective of Process Planning: The chief of process planning is to augment and modernize the business methods of a company. Process planning is planned to renovate design specification into manufacturing instructions and to make products within the function and quality specification at the least possible costs. This will result in reduced costs, due to fewer staff required to complete the same process, higher competence, by eradicating process steps such as loops and bottlenecks, greater precision, by including checkpoints and success measures to make sure process steps are completed precisely, better understanding by all employees to fulfil their department objectives. Process planning deals with the selection of the processes and the determination of conditions of the processes. The particular operations and conditions have to be realised in order to change raw material into a specified shape. All the specifications and conditions of operations are included in the process plan. The process plan is a certificate such as engineering drawing. Both the engineering drawing and the process plan present the fundamental document for the manufacturing of products. Process planning influences time to market and productions cost. Consequently the planning activities have immense importance for competitive advantage.
Effect of process planning on competitive advantage: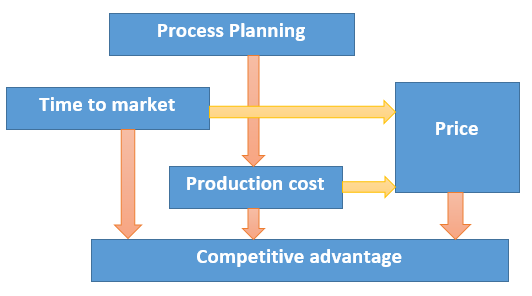
Principles of Process Planning
General principles for evaluating or enhancing processes are as follows:
- First define the outputs, and then look toward the inputs needed to achieve those outputs.
- Describe the goals of the process, and assess them frequently to make sure they are still appropriate. This would include specific measures like quality scores and turnaround times.
- When mapped, the process should appear as a logical flow, without loops back to earlier steps or departments.
- Any step executed needs to be included in the documentation. If not, it should be eliminated or documented, depending on whether or not it's necessary to the process.
- People involved in the process should be consulted, as they often have the most current information.
Process planning includes the activities and functions to develop a comprehensive plans and instructions to produce a part. The planning starts with engineering drawings, specifications, parts or material lists and a forecast of demand. The results of the planning are routings which specify operations, operation sequences, work centres, standards, tooling and fixtures. This routing becomes a major input to the manufacturing resource planning system to define operations for production activity control purposes and define required resources for capacity requirements planning purposes.
Process plans which characteristically offer more detailed, step-by-step work instructions including dimensions linked to individual operations, machining parameters, set-up instructions, and quality assurance checkpoints. Process plans results in fabrication and assembly drawings to support manufacture and annual process planning is based on a manufacturing engineer's experience and knowledge of production facilities, equipment, their capabilities, processes, and tooling. But process planning is very lengthy and the results differ based on the person doing the planning.
Major steps in process planning: Process planning has numerous steps to complete the project that include the definition, documentation, review and improvement of steps in business processes used in a company.
Definition: The first step is to describe what the process should accomplish. It includes queries like, what is the output of this process? Who receives the output, and how do they define success?, What are the inputs for the process?, Are there defined success measures in place - such as turnaround time or quality scores? And Are there specific checkpoints in the process that need to be addressed?
Documentation: During the documentation stage, interviews are conducted with company personnel to determine the steps and actions they take as part of a specific business process. The results of these interviews is written down, generally in the form of a flow chart, with copies of any forms used or attached. These flow charts are given to the involved departments to review, to make sure information has been correctly captured in the chart.
Review: Next, the flow charts are reviewed for potential problem areas.
Process planning in manufacturing may include the following activities:
- Selection of raw-stock,
- Determination of machining methods,
- Selection of machine tools,
- Selection of cutting tools,
- Selection or design of fixtures and jigs,
- Determination of set-up,
- Determination of machining sequences,
- Calculations or determination of cutting conditions,
- Calculation and planning of tool paths,
- Processing the process plan
Computer Aided Process Planning
Manufacturers have been following an evolutionary step to improve and computerize process planning in the following five stages:
Stage I - Manual classification; standardized process plans
Stage II - Computer maintained process plans
Stage III - Variant CAPP
Stage IV - Generative CAPP
Stage V - Dynamic, generative CAPP
Earlier to CAPP, producers attempted to triumph over the issues of manual process planning by basic categorization of parts into families and developing standardized process plans for parts families that is called
Stage I. When a new part is initiated, the process plan for that family would be manually recovered, marked-up and retyped. While this improved output but it did not enhance the quality of the planning of processes.
Computer-aided process planning originally developed as a device to electronically store a process plan once it was shaped, recover it, amend it for a new part and print the plan. It is called
Stage II. Other ability of this stage is table-driven cost and standard estimating systems.
Stage III: Computer-aided approach of variant CAPP is based on a Group Technology coding and classification approach to recognize huge number of part attributes or parameters. These attributes permit the system to choose a baseline process plan for the part family and achieve about ninety percent of the planning work. The schemer will add the remaining ten percent of the effort modifying or fine-tuning the process plan. The baseline process plans stored in the computer are manually entered using a super planner concept that is, developing standardized plans based on the accumulated experience and knowledge of multiple planners and manufacturing engineers.
Stage IV: It is generative CAPP. In this stage, process planning decision rules are developed into the system. These decision rules will work based on a part's group technology or features technology coding to produce a process plan that will require minimal manual interaction and modification.
While CAPP systems move towards being generative, a pure generative system that can create a complete process plan from part classification and other design data is a goal of the future. These types of generative system will utilize artificial intelligence type capabilities to produce process plans as well as be fully integrated in a CIM environment. An additional step in this stage is dynamic, generative CAPP which would consider plant and machine capacities, tooling availability, work center and equipment loads, and equipment status in developing process plans.
The process plan developed with a CAPP system at Stage V would differ in due course depending on the resources and workload in the factory. Dynamic, generative CAPP also entails the need for online display of the process plan on a work order oriented basis to cover that the appropriate process plan was provided to the floor.
There are numerous advantages of this type of process planning. It can decrease the skill required of a planner. It can reduce the process planning time. It can reduce both process planning and manufacturing cost. It can create more consistent plans. It can produce more accurate plans. It can increase productivity. Automated process planning is done for shortening the lead-time, manufacturability feedback, lowering the production cost and consistent process plans. Advantages of Computer-aided Process Planning include reduced demand on the skilled planner, reduced process planning time, reduced process planning and manufacturing cost, created more consistent plans, produced accurate plans, increased productivity, increased high flexibility, attained high efficiency, attained adequate high product quality and possibility of integration with the other automated functions and systems.
Manufacturing Process Planning delivers essential process planning potential for all manufacturing industries. Using Manufacturing Process Planning, process planners can powerfully create and authenticate the original process plan using the product structure from product engineering, modify the plan to specific requirements, and link products and resources to the steps of the plan.
To summarize, Process Planning is important action in a production enterprise that verifies which processes, materials, and instructions will be used to produce a product. Process planning describes a manufacturing facility, processes and parameters which are to be used to change materials from a primary form to a predetermined final stage.